AGV –
Automated Guided Vehicle
Automatic Steering Control through Camera Guidance
Steering of the greatest precision, placement of the highest accuracy, safety of the highest degree.
More Videos
AGV in production line with 2 tugs
The principle: A camera scans continuously the floor below the Mototok. A solid line is recognized as the guiding line. The camera recognises the position and curvature of the guiding line to within 3 mm. It reacts with control signals that are led to the drive wheels. A steering is initiated – Mototok follows the line.
Bar codes on the floor let the Mototok automatically brake down or speed up, stop or change the course in case of a junction.
On production lines during aircraft manufacture, Mototok is a versatile tool that can be used with great flexibility. During assembly, Mototok automatically moves the aircraft fuselage to the individual assembly points. In very space-restricted production environments, two synchronized Mototoks may also be used, as shown in this example of a production hall design. In addition, we work together with you to develop the optimal path through your hall.
Automatic Success.
No Problems, No Mistakes.
Automatic Steering Control.
Millimeter Accuracy.
Erase Human Error.
Automated Guided Vehicle
Steer with unbelievable Precision.
Ultimate Safety
Mototok is the right tug for the tightest turn anyway, but you might need even greater safety and programmability for your field of application. That's why we worked out our automated guided vehicle steering option - and it's accurate beyond comparison.
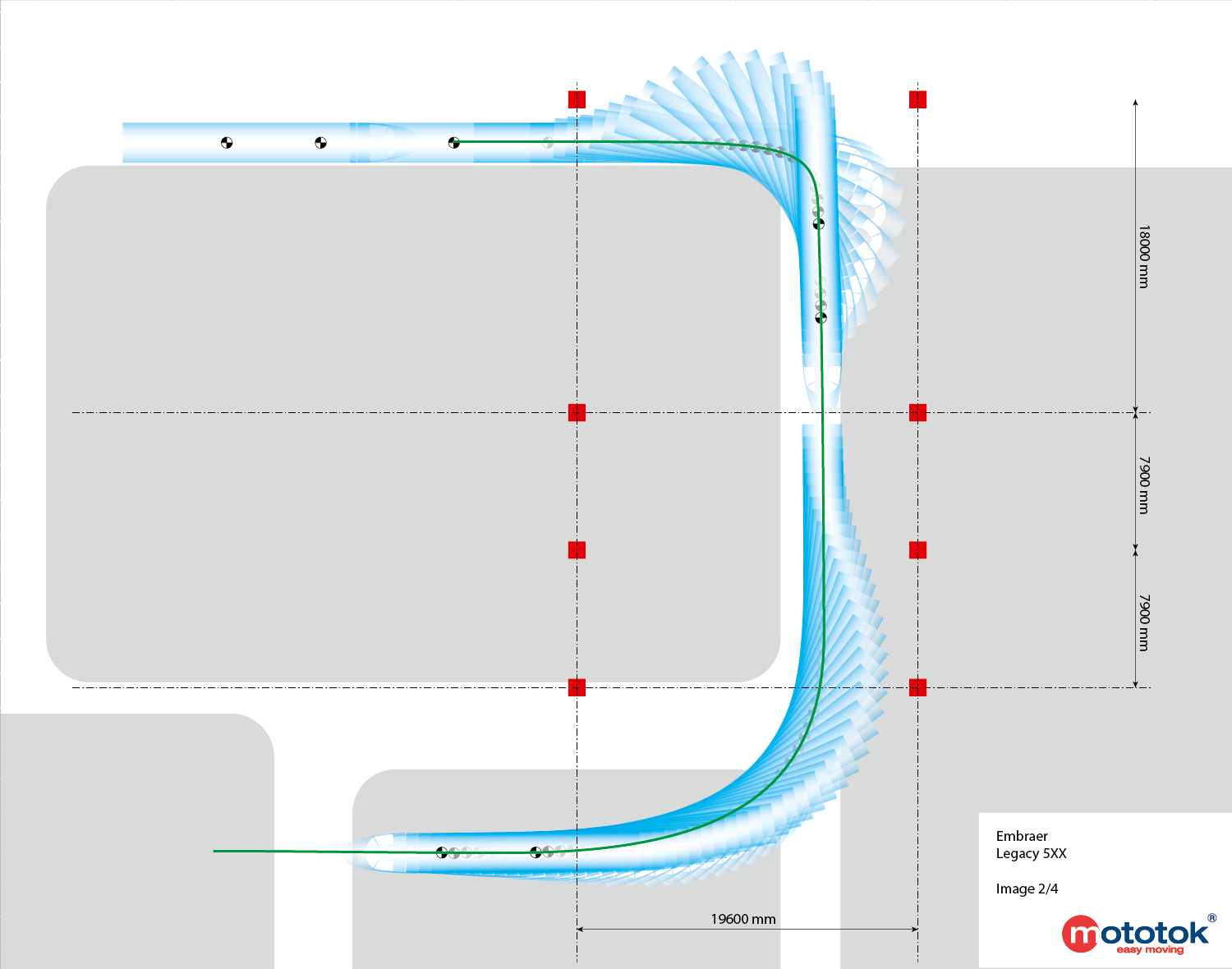
Dead-On Placement
E.g. on production lines during aircraft manufacture, Mototok is a versatile tool that can be used with great flexibility. During assembly, Mototok automatically moves the aircraft fuselage to the individual assembly points.
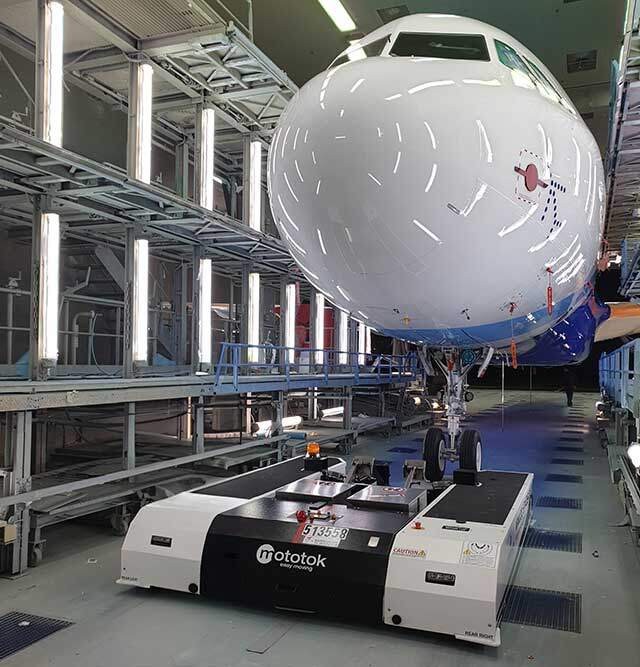
Still too tight? Use multiple tugs simultaneously
With very constricted room available, more than one synchronized Mototoks can be utilized, and if need be, we're happy to work with you to develop the optimal path through your hall.
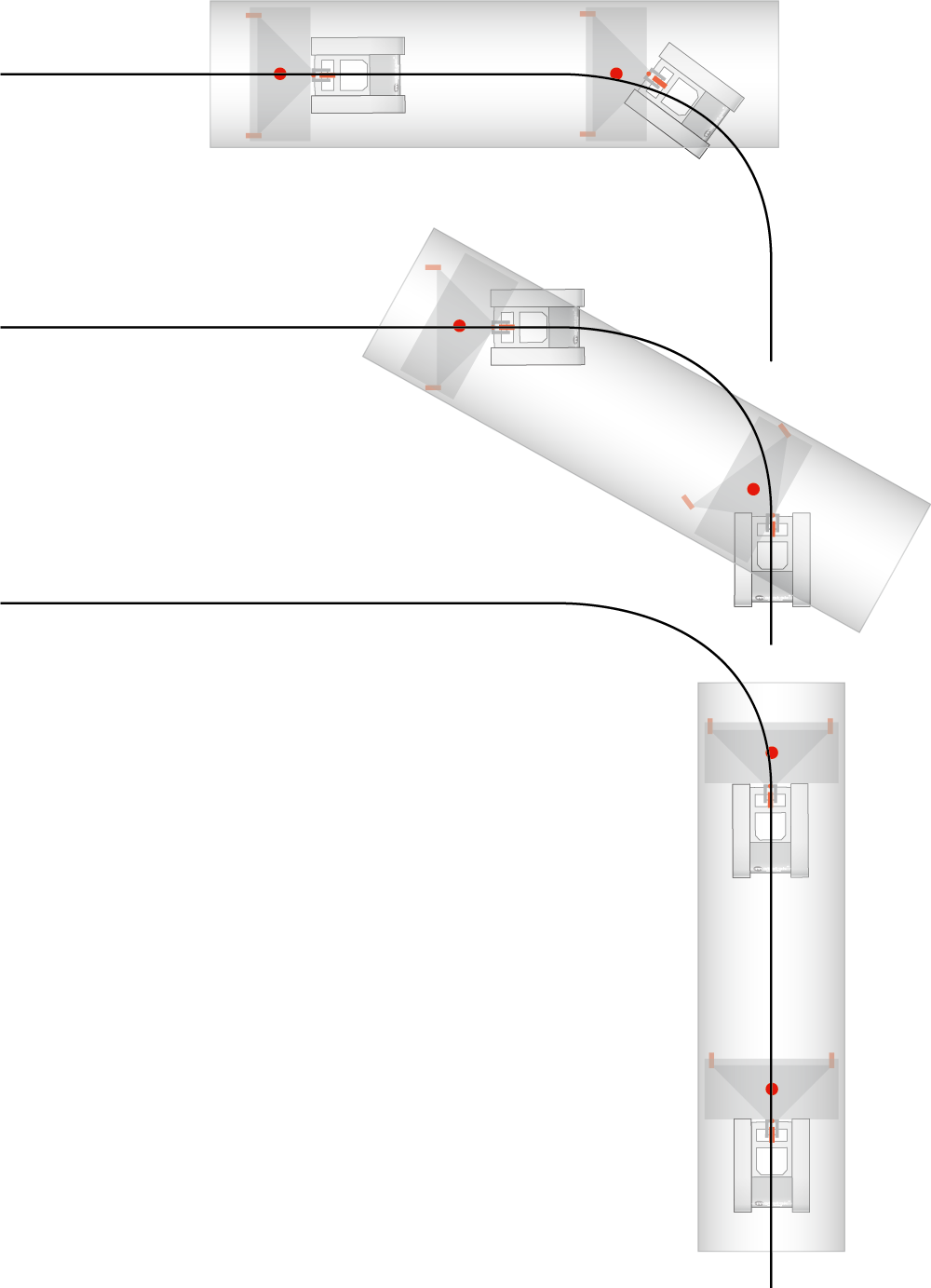
HIGHLY IMPROVED PROCESSES
So this is how it works: A camera continuously scans the floor below the mototok, where a solid line of defined width is recognized as the guiding line. The camera recognises the position and curvature of the guiding line within a range of 3 mm. If there is a variation in parallelism, it reacts with control signals that are led to the drive wheels. By means of different rpms of the two drive wheels, steering is then initiated – mototok follows the line with millimeter accuracy.
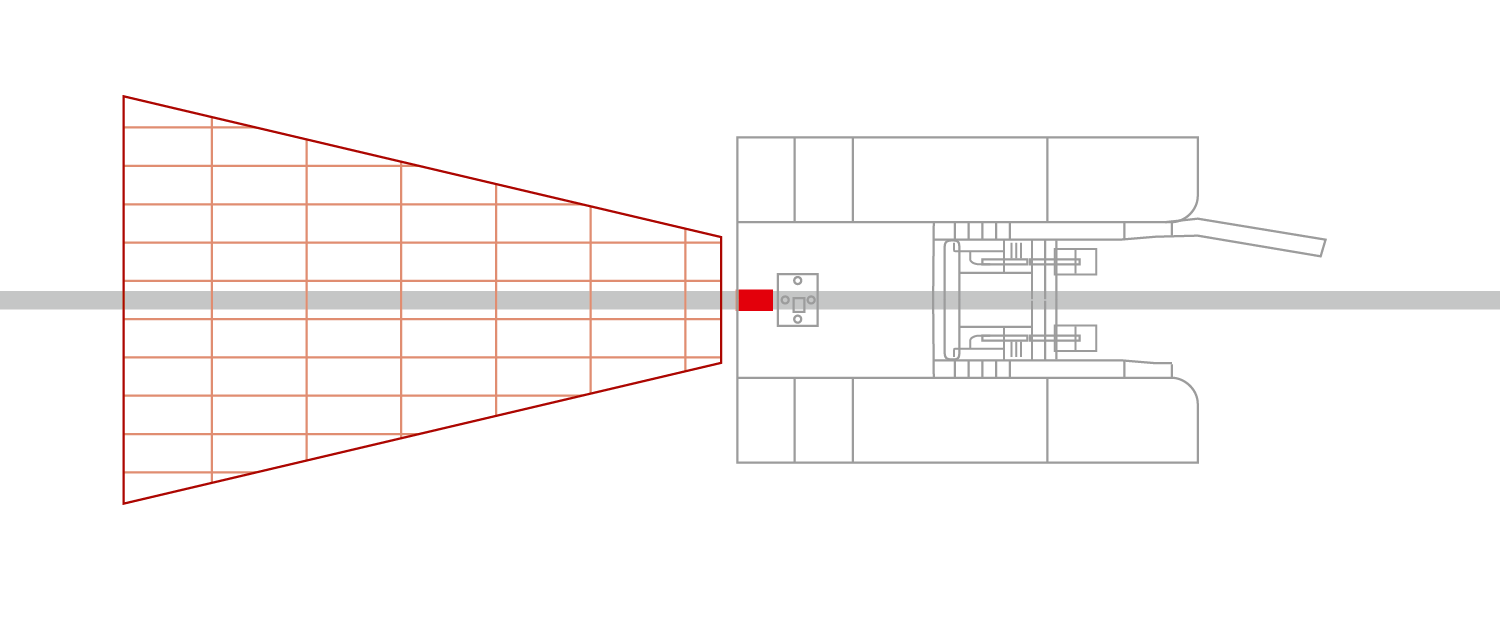
UTILIZE COMMANDS FOR FULL AUTOMATIZATION
Using bar codes installed on the hall floor, stop commands can be triggered, nose wheels automatically disengaged, and junctions taken into account.
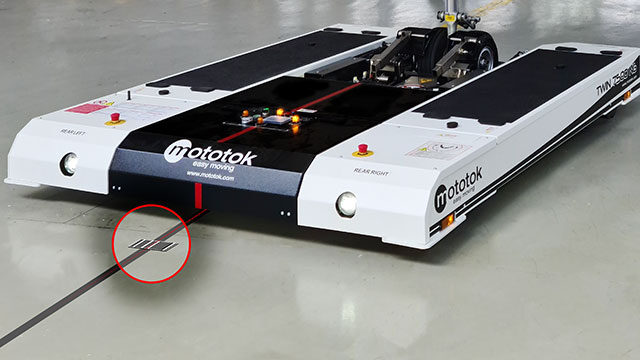